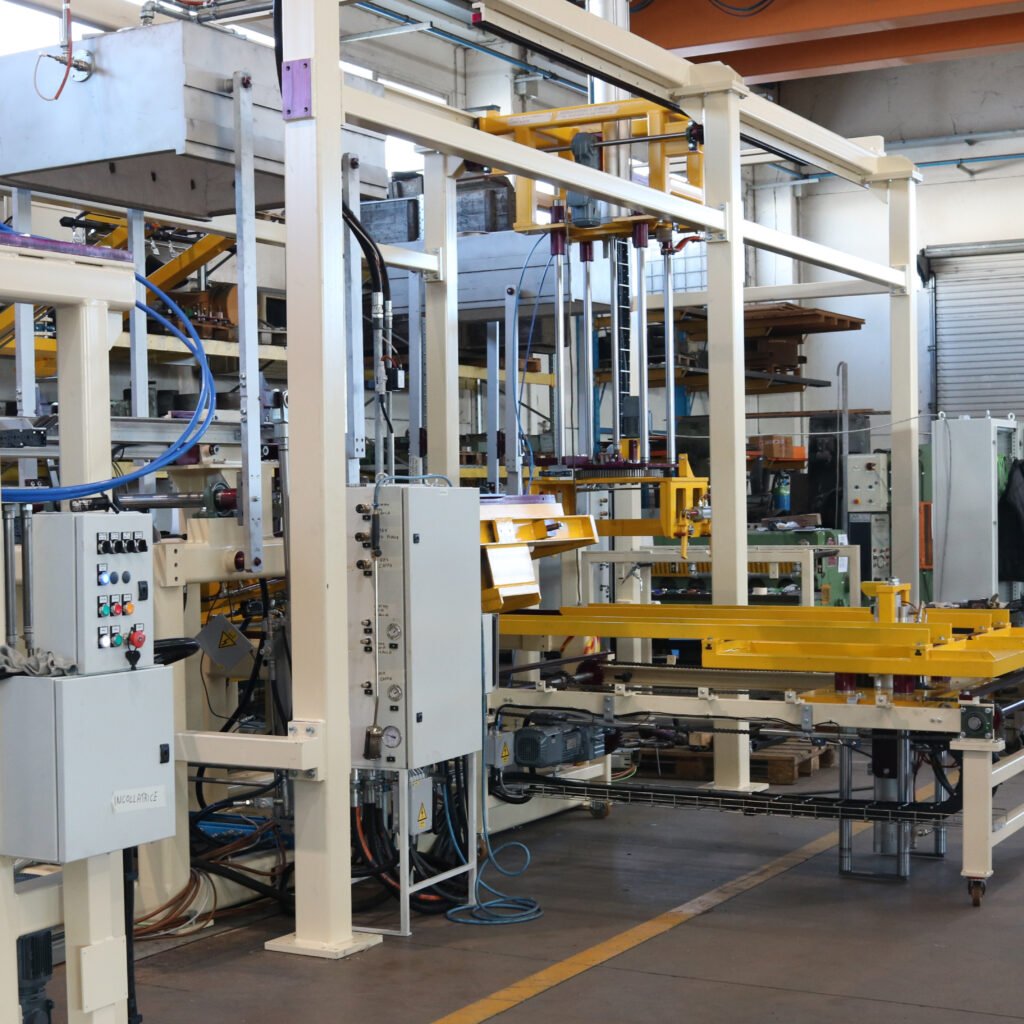
Introducing automation to boost productivity and improve the working environment
The foundry in Ljungby is facing a change in the form of automation. A new shell-forming cell will be implemented and automate steps in mould production. The innovation promises to boost productivity and improve the working environment. The shell-forming cell will bring many advantages to the shell-making process and increase the number of shells made per shift.
– Foundries are usually extremely traditional with low margins, which means that it can be hard to invest in automation. But developing production with the help of digitalization and automation is the future. The possibility to make this investment now opens more opportunities to continue this journey forward, says Emma Sundqvist, COO of Combi Wear Parts.
Positive effects
The shell-forming cell itself is quite a conventional method, but what is different about this cell is the setup of automation around it.
– In our current machine, setup time becomes very long due to handling and heating of the pattern – a process that takes up to three hours today. The new shell molding cell consists of a preheating station, which means that heating can be done in parallel while the machine is running. This way, we shorten the setup time from three hours to ten minutes. I have not seen this type of cell anywhere else before, says Emma.
Automation will also lead to an improved working environment, which is something that is high on the agenda for Combi Wear Parts.
– It is important to remove the possibility to work in an unhealthy way and constantly look for ways to improve the working environment. With automation, we reduce the risk of injuries, says Emma.
Keeping up with development and automation in the factory will also make the company a more attractive employer.
– We are many employers wanting to recruit skillful people and therefore we need to be in the forefront when it comes to the working environment and our ability to offer interesting job positions, Emma says.
Soon to be installed
The process is in full swing. The equipment will be completed in May, and then the cell can be assembled at the foundry. We have chosen two different suppliers for the equipment. The molding machine, glue station, and preheating station have been manufactured in Italy. The automation, including a robot, comes from a Swedish supplier.
– The shell-forming cell expects to be complete and ready for test runs in June. Then the machine needs to be fine-tuned, and the staff needs to learn to program and operate it before we can go at full speed, Emma says.
A starting point for the future
The automation project has been received very positively by all staff, who look forward to easier and more enjoyable work.
– We believe that giving opportunities for our employees to develop in their roles increases the overall satisfaction at our workplace, and in turn gives us a more skillful and committed staff. This investment is a starting point for the future and will be positive both from a work environment perspective and an efficiency perspective. Our strategy says that we should double our current production rate, and this is a natural step to succeed and meet that strategy, Emma explains.