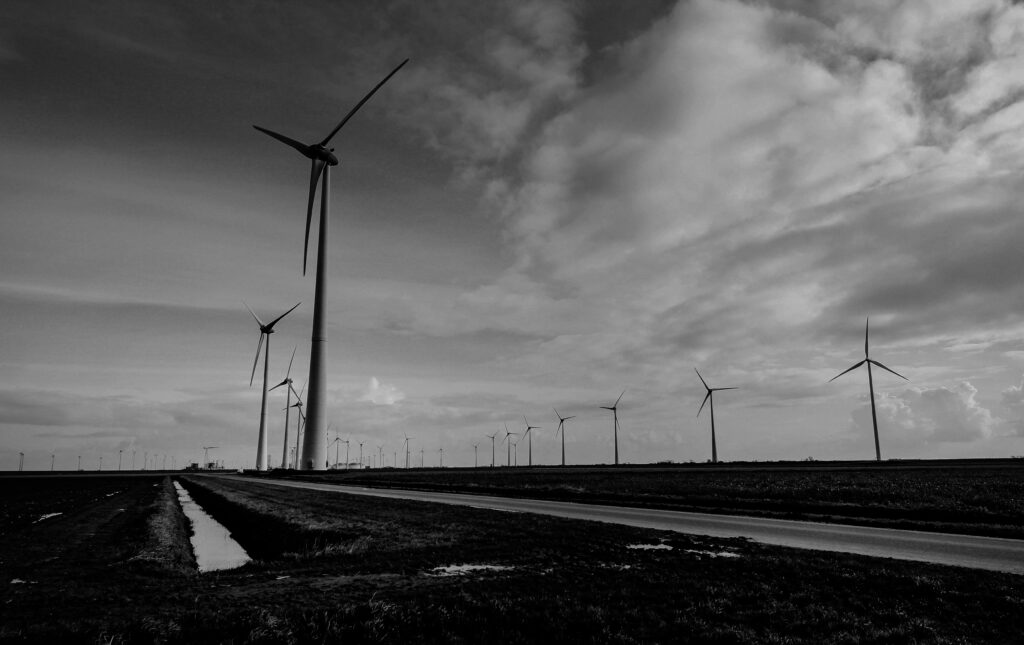
Why we are a good choice for the environment
At Combi Wear Parts, sustainability is at the heart of our operations. We exclusively use recycled steel scrap from Swedish steel manufacturing companies, which is melted and processed into our final products. Furthermore, we encourage to return and recycle used wear parts, promoting recycling at both ends of the product lifecycle.
While our products might cost a bit more, they offer superior function, performance, and quality. Additionally they provide the benefits of environmental sustainability and a cleaner conscience.
Energy-Efficient Production
Melting down scrap to cast world-class wear parts is energy-intensive, requiring 740 kWh to produce 1,000 kg of finished products – the same amount of energy a typical Swedish home uses during a cold winter month. Combi Wear Parts has committed to using only renewable energy, generated by Swedish water and wind power, significantly reducing our climate impact compared to other foundries worldwide.
Lower CO2 Emissions
Independent studies highlight Sweden’s lower CO2 emissions in steel production. Producing 1,000 kg of steel castings in Sweden generates less than 100 kg of CO2 emissions. In comparison, the same amount of steel produced in other countries results in much higher emissions.